Calibration VS Validation an Overview
The pharmaceutical industry has a big job: making sure medicines are safe and work well for millions of people around the world. To do this, they have strict rules to follow called quality control. Calibration and validation are super important parts of this process. They help make sure medicines are safe and effective, protecting not just the products, but also people’s lives. In pharma industry, Calibration ensures the measurement accuracy of an instrument meets a known standard.Validation ensures a system satisfies its stated functional intent.
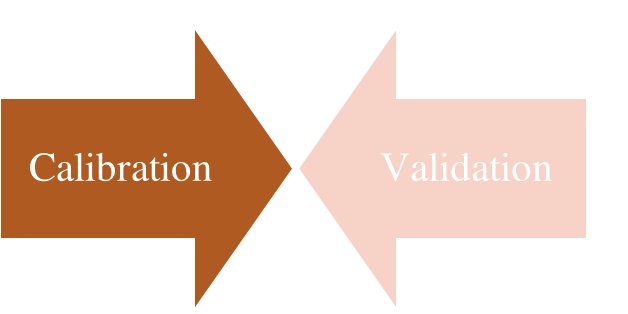
Calibration
Calibration in the pharmaceutical industry is the process of adjusting and verifying the accuracy of instruments and equipment used in various stages of drug manufacturing, testing, and analysis. This adjustment ensures that these instruments provide precise and reliable measurements, aligning with established standards.
In simpler terms, calibration makes sure that the machines and tools used to make medicines are accurate and give the right results. It involves comparing the measurements they give with known standards and making any necessary adjustments to ensure they’re correct.
Calibration is crucial in pharmaceutical manufacturing for several reasons:
Accuracy: Accurate measurements are essential in producing medications with the correct dosages and compositions. Calibration ensures that instruments provide precise readings, minimizing the risk of errors in drug formulation.
Compliance: Regulatory authorities such as the FDA require pharmaceutical companies to maintain calibrated equipment as part of Good Manufacturing Practices (GMP). Compliance with these regulations is necessary to ensure the safety, efficacy, and quality of pharmaceutical products.
Quality Assurance: Calibration helps maintain consistent product quality by ensuring that manufacturing processes remain within specified tolerances. This consistency is vital for producing reliable and effective medications.
Risk Mitigation: Inaccurate measurements can lead to production errors, resulting in wasted materials, production delays, or even compromised product quality. Calibration helps mitigate these risks by identifying and correcting deviations in instrument performance.
Validation
In the pharmaceutical industry, validation refers to the process of ensuring that systems, processes, and procedures are designed and operated in a way that consistently produces results meeting predetermined specifications. This validation process is crucial for confirming that the pharmaceutical manufacturing and quality control processes are reliable, effective, and compliant with regulatory standards.
Validation is essential in pharmaceutical quality control for several reasons:
Assuring Product Quality: Validation ensures that every step of the manufacturing process, from raw material handling to packaging, is meticulously controlled and monitored to produce high-quality pharmaceutical products. This helps prevent defects and ensures that medicines are safe, effective, and of consistent quality.
Compliance with Regulations: Regulatory authorities, such as the FDA and EMA, require pharmaceutical companies to validate their manufacturing processes to ensure compliance with Good Manufacturing Practices (GMP) regulations. Validated processes demonstrate that the company is meeting regulatory requirements and producing drugs that meet safety and efficacy standards.
Risk Reduction: Validation helps identify potential risks and weaknesses in the manufacturing process early on, allowing companies to implement corrective actions to prevent issues such as contamination, cross-contamination, or product variability. By minimizing risks, validation contributes to improving product safety and reducing the likelihood of product recalls or regulatory sanctions.
Enhancing Efficiency: Validated processes are more efficient and reliable, leading to improved productivity and reduced waste. By ensuring that equipment and procedures are optimized and consistently deliver the desired results, validation helps streamline manufacturing operations and minimize downtime.
Summary
validation is a critical component of pharmaceutical quality control that ensures manufacturing processes are robust, reliable, and compliant with regulatory standards. By validating processes, pharmaceutical companies can assure product quality, minimize risks, enhance efficiency, and maintain consumer trust in the safety and efficacy of their products.
Feature
- Focus
- Process
Calibration
- Measurement accuracy
- Adjustment to a standard
Validation
- System performance
- Testing against intended function